Inventory reconciliation for companies using production orders is not complete without discussing production order work-in-process (WIP). Flushing methods can impact when entries are made to WIP as can subcontract purchase orders. The following flow is based on manual flushing.
Consumptions against a production order add dollars to WIP (debit for you accountants) and reduce amounts for component inventory (accounting credit). This is the reason you have two accounts in Inventory Posting Setup, one for inventory and one for WIP. It is recommended that you use two different general ledger account.
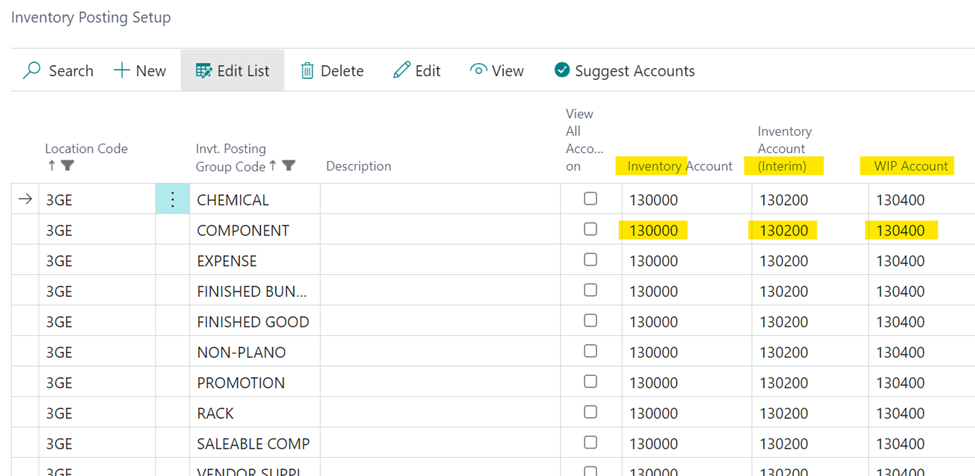
Capacity is machine and people time from work centers, as well as, associated indirect costs and overhead from work centers. Work centers are identified in routings and routings are attached to produced items or stockkeeping units. When entries are posted to routing steps WIP is increased with associated general ledger accounts reduced.
At this point in the production order, consumption and capacity have increased WIP. This can be seen on the Prod. Order WIP report.
Output of finished product will reduce WIP (credit) and increase interim inventory (debit.) The idea here is that as product is finished, WIP is cleared. However, there are typically amounts left in WIP when a production order is finished. Changing the status on a production order from released to finished will clear WIP and interim inventory (credits) and finalize finished inventory (debit).
Many times, I receive a call that the WIP report is still showing values in WIP for finished production orders. The answer here is always run Adjust Cost before running the WIP report to make sure that the values from those finished production orders are handled.
Using forward flushing or back flushing, as I mentioned before, changes the timing of consumption entries for when WIP entries are posted. Forward flushing will post all consumption to WIP when the order is released. Back flushing will post all consumption to WIP when the order is finished and since the order is finished WIP will be cleared.
Subcontract production orders record output of finished inventory when purchase orders are received. It is common for production orders to be finished before vendor invoices are posted. Of course, the preference is to post vendor invoices before finishing production orders. Either way, Business Central correctly handles WIP and inventory…. it’s all about timing.
Bottom line is Prod Order WIP should balance to the associated General Ledger Account for WIP. Notice that from the menu, you choose Prod Order WIP report, but the report title is Inventory Valuation WIP.
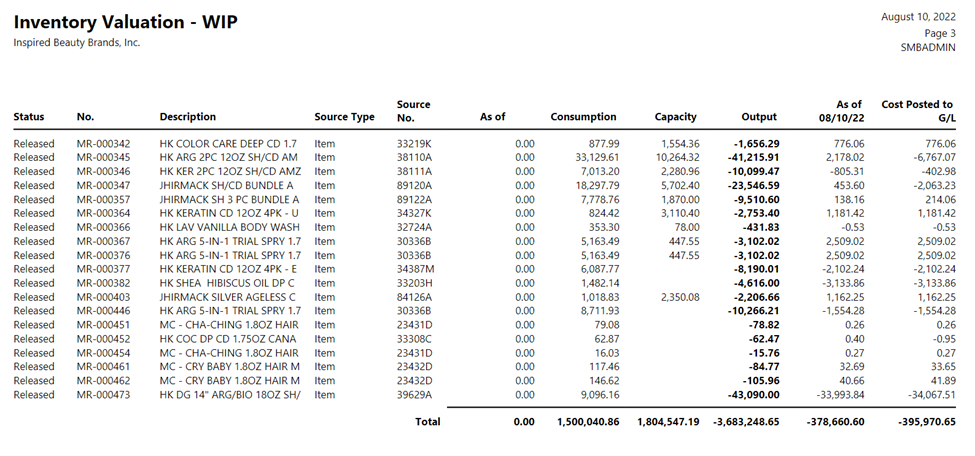
It is recommended that you run the Prod Order WIP report for Finished status and make sure that cost posted to GL is zero. If this is not zero, it’s a reminder to run Adjust Cost.
When running the Prod Order WIP report, you really want to run for Released Status and be sure to enter your As Of date so that you are getting the values for the date desired.